超细粉碎
至关重要的工艺选择
材料的颗粒度是影响和决定其在终端应用中的性能优劣的最重要物理指标。而粉碎则是当今最常被使用以获取目标颗粒度的关键工艺。伴随着材料应用面的不断拓展和深入,达成稳定高效获取超细颗粒也成为了众多先进材料制备过程中的重要目标。粉泰克的工艺专家深谙超细粉碎的核心机理,结合我们针对不同材料的丰富应用经验,我们将帮助您选择最适合您目标的超细粉碎工艺,以达成高品质材料的生产。
Scalable, continuous production process: Efficient synthesis with less by- and waste products
Production of Our Lithium Iron Phosphate
For more than 10 years IBU-tec has been involved in the development and production of LFP cathode material. The starting materials first pass through spray drying, are refined in a rotary kiln and then milled: an excellent production performance with high quality.
流化床气流磨
流化床气流磨是当今最先进的针对微米级至亚微米级颗粒的干式粉碎技术,通常可企及0.5微米到50微米的粒度范畴。在该类气流磨中,带有压力和温度的气流被引入研磨腔后,驱动原料颗粒高速运动而产生颗粒间的相互碰撞,从而产生粉碎效果以达到减小颗粒粒度的目的。基于该机理,流化床气流磨中的粉碎过程不存在颗粒和任何机械部件的碰撞,因此有效避免了在其他粉碎工艺中由于颗粒和机械部件碰撞而产生的机械部件磨损以及随之而来的对产品的污染。此外,流化床气流磨中带有动态空气分级轮,用户通过调节分级轮转速,即可灵活快速获取不同颗粒度的产品。
IBUvolt® LFP400 | IBUvolt® LFP402 | |
Particle size d50 [µm] | 11.1 | 1.2 |
Tamped density [g/cm³] | 1.0 – 1.4 | 0.6 – 0.9 |
Electrode density [g/cm³] | 2.3* | ≥ 2.5* |
Specific capacity [mAh/g] | ≥ 149 | ≥ 159* |
Data sheet | Download |
优点
- 精确的最大粒径控制,绝无不合格粗颗粒
- 更狭窄的成品颗粒度分布
- 极为稳定的产品批次间结果
- 单机大产能
- 粉碎过程无温升,适用于热敏性产品
- 可粉碎所有硬度的产品
- 极低的杂质引入
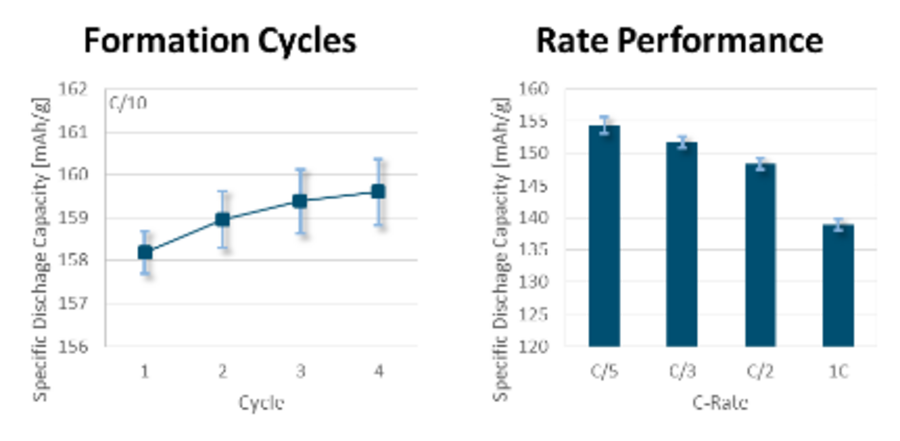
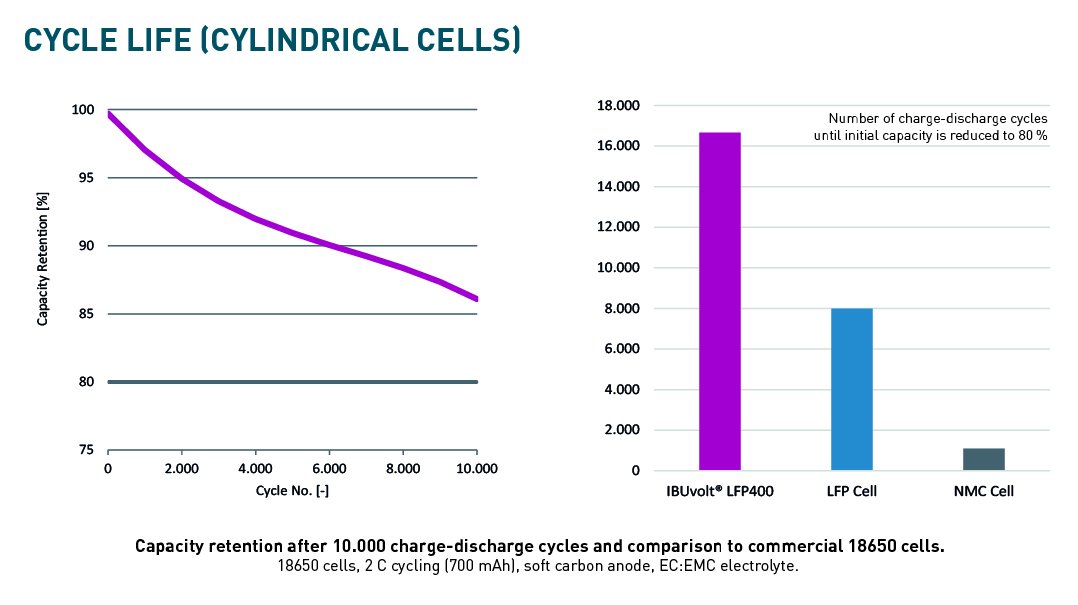
IBUvolt® LFP400 – Long Life and Cycle Stability
For more than 10 years IBU-tec has been involved in the development and production of LFP cathode material. The starting materials first pass through spray drying, are refined in a rotary kiln and then milled: an excellent production performance with high quality.

转子冲击磨
转子冲击磨是应用最为广泛的精细粉碎装置之一,其可涵盖的粒度范围通常在30微米到2毫米左右。冲击磨内部的研磨转子和定子可根据不同应用和要求灵活设计并快速切换。待粉碎的颗粒进入磨机后,在转子带动下高速运动,在冲击力、剪切力和摩擦力的作用下被粉碎成合适的粒度。不同的定/转子结构,转子运行速度以及同下游工艺装置的结合匹配都会对最终的粉碎效果产生直接影响。
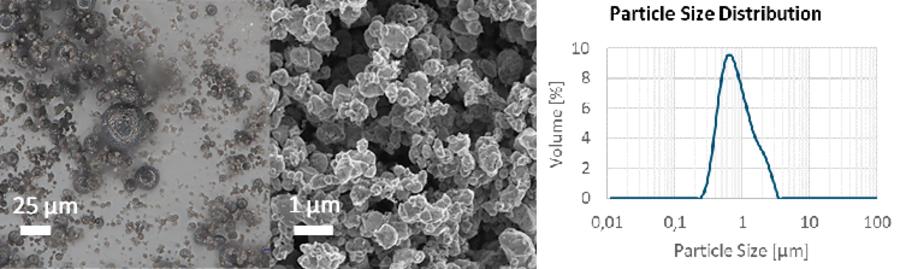
Compacting Properties
For more than 10 years IBU-tec has been involved in the development and production of LFP cathode material. The starting materials first pass through spray drying, are refined in a rotary kiln and then milled: an excellent production performance with high quality.
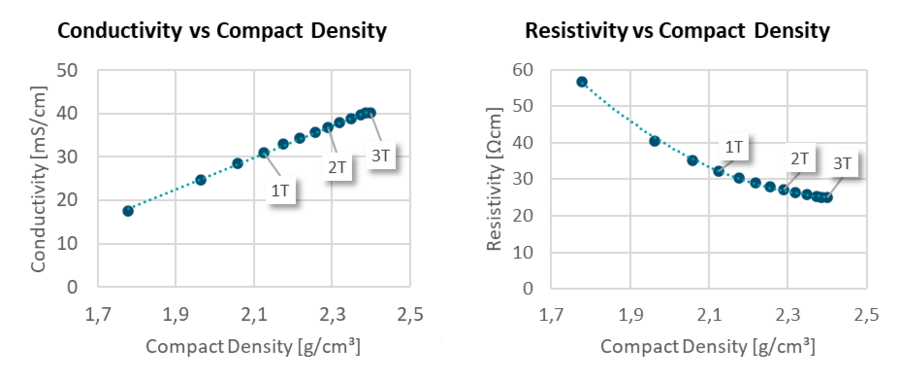
Background on Lithium Iron Phosphate Batteries
Energy storage systems are a valuable key technology for not having to rely on the use of fossil raw materials for energy production and being able to use other sources, such as wind power and photovoltaic systems. Currently available storage systems are largely based on the proven lithium-ion battery technology. Lithium-ion batteries consist of four basic components that make up the battery's cells: Cathode, Anode, Separator and Electrolyte. IBU-tec has many years of experience in the production of lithium iron phosphate cathode material (LFP or LiFePO4).
When charging a lithium-ion battery or lithium-ion accumulators, lithium ions are transported through the electrolyte layer from the cathode to the anode. In the anode, which is often made of graphite or other carbon-rich materials, the reversible
ntercalation of the lithium takes place with the absorption of electrons. When the battery is discharged, this process is reversed. The lithium-rich anode layer releases electrons and the resulting lithium ions are transported to the cathode. The resulting current flow can be used by electrical consumers. This cycle can be repeated several times in rechargeable batteries, although certain memory effects are inevitable. The higher the quality of the battery and the materials used in it, such as lithium iron phosphate, the longer the service life can be.
Lithium iron phosphate is becoming increasingly important as a cathode material in modern batteries. Depending on the end application and field of use – be it in the field of e-mobility or in stationary energy storage – different requirements arise.
The designation LFP is derived from the empirical formula LiFePO4. LFP cathodes are free of the heavy metal nickel and the critical raw material cobalt. Compared to other cathode materials, LFP also shows advantages in durability and safety.